A startup spun out of a discovery from the Australian National University (ANU), Samsara, is commercialising its plastic-recycling tech, which lets it take plastic from landfill and break it down to a base form, which can be used to make new plastic products.
For retailers making products using plastic the technology will allow them to use 100% recycled materials in their goods as a selling point.
Currently, almost all of Australia’s recycling is mechanical instead of chemical and requires high-quality clean plastic waste collected from container deposit schemes. That gets broken up into pellets which need specialising manufacturing procedures to be moulded into goods and isn’t perfect for every use.
For example, consumer brands bottling carbonated drinks can’t use the recycled materials produced in Australia.
Different coloured hard plastics can’t be recycled, nor can plastics that have degraded or deteriorated.
Samsara’s method, which makes use of a computer-designed enzyme which breaks down the plastic from polymers to monomers. Polymers are essentially chains of monomers that are joined together.
The enzymes do not affect any of the other materials in the process and can break down products at room temperature.
When making new plastic products manufacturers mostly use monomers, or ‘virgin’ plastic that has not been used before.
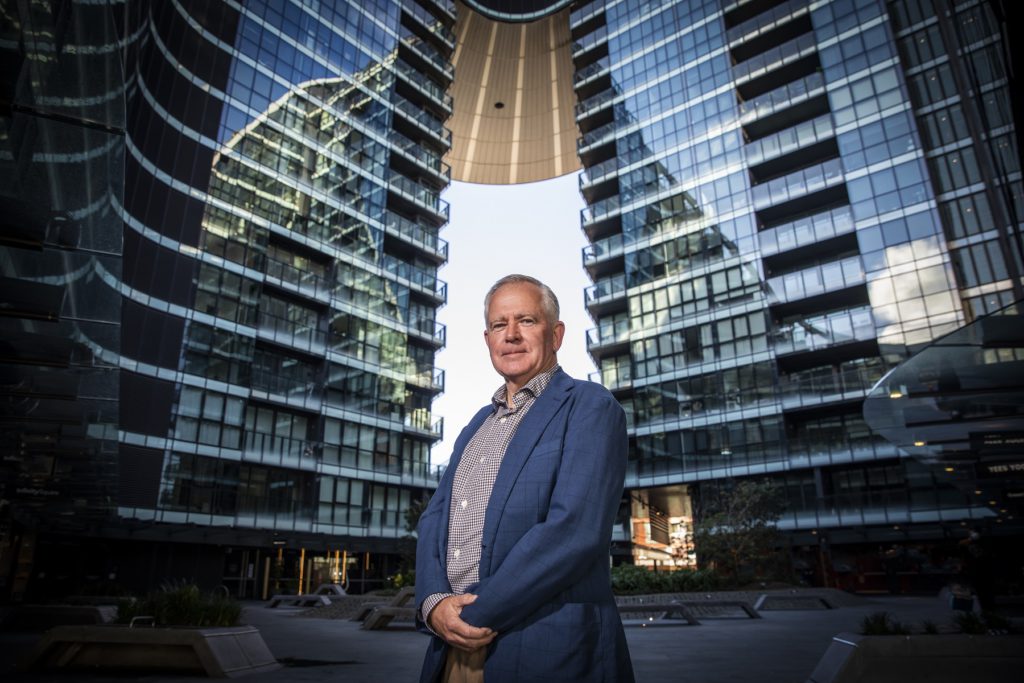
Samsara CEO Paul Riley tells Retailbiz, “The new recycled plastic is identical to a virgin product.
“We’re really excited about the technology, the introduction of an infinite recycling closed loop for plastics is incredibly exciting.”
The plastic waste is placed into large vats and broken down by the enzymes in under an hour, without any heating needed. Other chemical processes take between 10 and 20 hours, says Riley.
The speed of the process and energy efficiency means that the company will be able to sell its recycled plastics at the same price as other recycled plastics on the market, according to Riley.
At the moment Samsara is able to produce recycled plastic at a kilogram-scale level. To get the company to industrial scale production, it has been awarded a $568,491 grant from the federal government, with additional investment from its partners — including Woolworths — bringing that figure up to $1.14m.
It’s currently undertaking commercial testing of its monomers, and has produced plastic tested against the specifications of major FMCG companies. It’s new facility, which it is deciding the jurisdiction for, will be able to produce 20,000 tonnes yearly.
“We expect to have our first product on shelf in Q1 2023, and Woolworths has committed to take 5,000 tonnes of our resin. They’ve supported us in the development phase.
“It will be available to other packaging or plastic users at the same time,” says Riley.
The technology is most advanced for PET plastics, but will have a nylon enzyme available at the end of the year, followed by polyurethane, polycarbonate, LDPE and HDPE.
“We will be able to process the mixed bail of plastics that ends up at the local tip,” says Riley.
Considering some 400 million tonnes of plastic come to market every year, with only 20% currently able to be recovered and recycled in Australia, there’s a huge opportunity for the company to grow.
Featured Image: A plastic polymer PET bottle (left) and pure monomer (terephthatic acid) obtained after the plastic degradation process (right). Photo credit: Research School of Chemistry/The Australian National University.